Modelli per la produzione di prodotti e servizi
Non esiste organizzazione che possa riposare sugli allori.
Ad esempio, quanto siamo pronti a cogliere con successo tutte le opportunità offerte dall'Industria 4.0?
Le opportunità di migliorare le prestazioni aziendali non finiscono mai, perché, anche se ho raggiunto buoni livelli di efficienza, devo stare attento a che non siano cambiate le richieste del mercato. Allora devo decidere se cambiare per piccoli passi o non siano richiesti interventi radicali sui processi
Dal punto di vista del processo logistico produttivo, non distinguiamo fabbricazione di prodotti o erogazione di servizi: esistono esigenze del cliente che devono essere soddisfatte, sia con servizi adeguati, sia con strumenti, prodotti e accessori idonei alle funzioni richieste.
Aumento dell’efficienza
L’Overall Equipment Efficiency è l’indicatore principe che fornisce le priorità sugli interventi da eseguire nel processo. Abbiamo interventi che migliorano velocità, qualità e affidabilità, insieme
Clienti soddisfatti
Uno dei servizi più apprezzati dai clienti, oggi, è la puntualità: promessa una data, non si può arrivare in ritardo. Rimuoviamo i vincoli come il lungo setup, le rilavorazioni e i mancanti per rispettare le scadenze
Maggiore flessibilità
I clienti sono diversi e il mix delle loro richieste cambia ogni momento. Realizzare il mix richiesto in tempi brevi si traduce in una significativa riduzione dei costi di gestione della produzione
Guarda i risultati di un intervento 5S che abbiamo condotto su linee di assemblaggio manuali
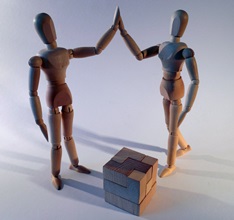
Quali sono le aree di miglioramento potenziali
Quali sono le aree di miglioramento in produzione.
Chi lavora nel processo logistico produttivo è responsabile realizzare il programma di produzione che gli viene consegnato. Per riuscirci, utilizza 3 leve fondamentali di organizzazione e gestione:
- Personale operativo;
- Macchine, impianti e attrezzature;
- Materie prime e semilavorati.
Intervenire su questi elementi ha un effetto immediato sul bilancio aziendale e sulle prestazioni valutate dai clienti.
Velocità di risposta alle richieste dei clienti
Il sistema produttivo può essere visto come un fluido in cui persone e materiali si muovono; se il fluido ristagna in qualche angolo dei magazzini o dei reparti, significa che non sta costruendo valore per i clienti.
Tahijchi Ohno ha codificato 7 categorie di attività che sprecano le energie delle risorse produttive; per rendere veloce il processo occorre rimuovere le cause che, oggi, impediscono di realizzare un vero flusso di materiali e persone all'interno del processo manifatturiero o di erogazione dei servizi.
Il modello della Lean Production è rivolto proprio a rimuovere gli impedimenti alla creazione di una produzione a flusso, con soluzioni tecniche ed organizzative molto efficaci e che abbiamo applicato presso tutti i nostri clienti.
Flessibilità al mix e ai volumi richiesti dal mercato
È una misura di quanto il processo produttivo sia adeguato al mercato che deve servire. Quando il mercato cambia, allora anche l’assetto di gestione del processo manifatturiero deve trovare nuovi punti di equilibrio fra riduzione dei costi e livello di servizio al cliente.
Di sicuro, se l’assetto del processo produttivo è uguale a quello che serviva il mercato di 10 anni fa, allora non è più adeguato a rispondere alle mutate esigenze dei clienti.
Su questo tema conta molto la capacità di realizzare pochi esemplari di prodotto alla volta: quanto pochi? La misura la fornisce il mercato, cioè la quantità che il mercato chiede nel brevissimo periodo.
Ciò si persegue, ad esempio, con interventi di:
- riduzione dei tempi di setup;
- addestramento delle maestranze a condurre impianti e macchine di diversi reparti;
- riprogettazione dell’assetto fisico dei reparti (layout), pensato per servire meglio il mercato;
Aumento dell’efficienza delle risorse produttive
Significa utilizzare al meglio l’unica risorsa davvero scarsa e incomprimibile: il tempo. Per fortuna si può prevedere quanto se ne ha a disposizione e si possono trovare soluzioni per utilizzarlo al meglio.
Personale operativo che trasporta dei materiali, resta a guardare una macchina che lavora o controlla il lavoro degli altri, sta eseguendo delle attività che non aggiungono valore al cliente; allora perché le svolge?
Sono richieste dalle procedure operative aziendali perché non si sono trovate altre soluzioni più efficienti!
Una impianto a cui viene chiesto di realizzare più di quanto richiesto dai clienti (solo perché, altrimenti, macchina e operatore rimarrebbero fermi) o che lavora con programmi non industrializzati (materiali con troppo sovrametallo, percorsi e sequenze utensile non ottimizzati), genera uno spreco di tempo.
Materiali che sono lasciati in posizioni sempre diverse, che devono essere cercati al bisogno o che non sono standardizzati nella codifica e nelle distinte base, generano attività di ricerca, verifica e controllo sugli operatori addetti.
Le soluzioni a questi e ad altre problematiche di produzione esistono già e possono contemplare:
- metodologie veloci ed efficaci, quali, ad esempio, applicazione delle 5S, introduzione del controllo statistico dei processi, implementazione del Kanban per l’alimentazione dei reparti;
- interventi più completi e organici come, ad esempio, l’avvio di progetti di miglioramento continuo Lean Six Sigma, l’analisi parametrica e la standardizzazione dei cicli di produzione, il reengineering del processo produttivo volto alla sua trasformazione Lean