Il modello Lean
I soldi ci sono, ma li butti e non sai nemmeno bene dove.
Nonostante le rinunce, i tagli e i sacrifici, ancora non riesci ad aumentare i margini della tua azienda.
Fai un passo deciso e agisci direttamente sugli sprechi del sistema produttivo, eliminando tutto ciò che non aggiunge valore per i tuoi clienti.
La Lean ti porta a rendere il sistema produttivo più flessibile al volume e al mix di prodotti, in modo da poter realizzare il tuo prodotto/servizio in linea con la domanda, senza sprecare tempo e denaro in scorte, in capacità produttiva non utilizzata e in attività di gestione (movimentazioni, controlli, …) altrimenti inutili.
Si riducono i costi
Qualsiasi spreco ha un costo e la sua eliminazione porta ad eliminare quel costo. Il nemico n. 1 della Lean è lo spreco di energie, lavoro, intelligenza.
Aumenta la velocità di risposta
Le attività inutili non aggiungono valore al prodotto, ma richiedono comunque tempo e fatica: eliminandole si riducono i tempi ed aumenta la velocità di risposta
Migliora la qualità del prodotto
Qualsiasi attività è a rischio di errore; anche le attività inutili lo sono: eliminandole si riducono le possibilità di errore e quindi si riduce la difettosità
Scopri come abbiamo aiutato VISA, che progetta, fabbrica e installa gruppi elettrogeni, ad attuare la sua trasformazione Lean
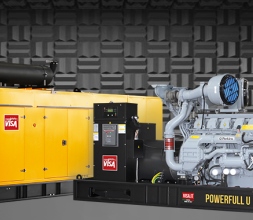
Come si applica il modello Lean
Il modello Lean corrisponde al Sistema di Produzione Toyota, sviluppato dalla Toyota Motor Company a partire dalla metà degli anni '60, che è stato completato, almeno nella versione a noi più nota, nel 1978; il termine “completato” non è del tutto appropriato in quanto, come tutte le organizzazioni, anche quella della Toyota è soggetta a continue modifiche e miglioramenti.
Non è esagerato affermare che si tratta di un nuovo e rivoluzionario sistema di organizzazione della produzione, che come tale si affianca a pieno titolo al sistema proposto da Taylor (gestione scientifica) e alla linea per produzione di massa realizzato da Ford, dei quali costituisce un’evoluzione naturale.
L’idea di fondo non è particolarmente originale: eliminare tutto quanto c’è di superfluo nella produzione, al fine di ridurre i costi.
Il superfluo è chiamato “spreco”, per evidenziarne l’aspetto negativo: ci sono sprechi di tempo quando le persone svolgono attività inutili, ci sono sprechi di spazio e di capitale quando si mantengono scorte di materiali o esubero di capacità produttiva.
Per evitare gli sprechi di cui sopra, si introduce il concetto di “Just in time”: si devono produrre output soltanto nelle quantità e nei tempi in cui gli stessi si rendono necessari.
L’obiettivo è di organizzare il sistema produttivo in modo che sia capace di soddisfare la domanda così come essa si presenta a livello mensile e giornaliero.
Tuttavia la domanda può essere molto variabile, sia nel volume totale che nel mix di prodotti, ed il seguirla mal si concilia con i tipici vincoli del sistema produttivo:
- capacità produttiva (vincoli al volume producibile)
- lunghi tempi di setup (vincoli al mix producibile)
Per affrontare questi vincoli la soluzione tradizionale è di accorpare la produzione in lotti, mentre la soluzione Lean porta a produrre “a flusso” in sintonia con la domanda, rimuovendo qualsiasi vincolo si frapponga a questa soluzione.
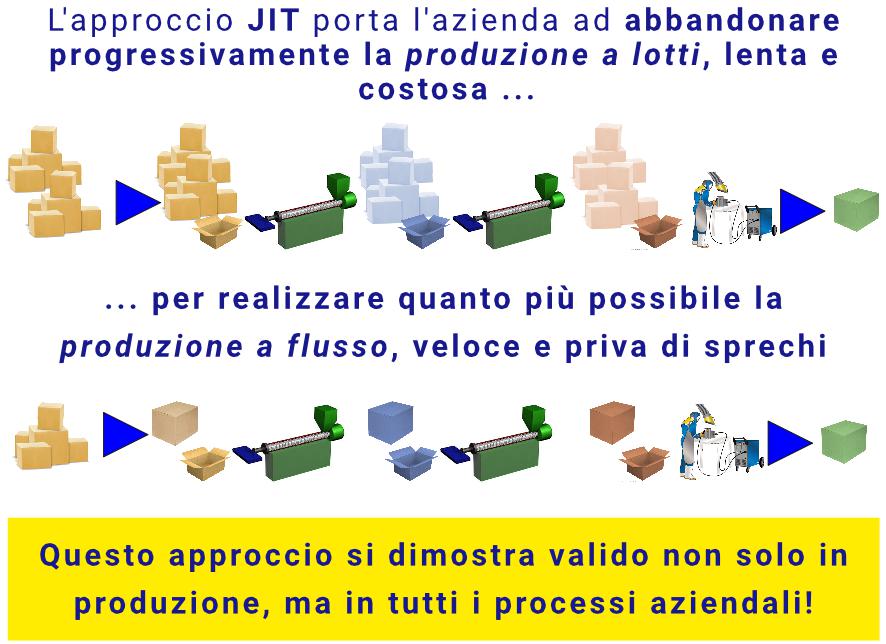
L’indicatore principale che misura la prestazione diventa il lead time, che corrisponde al tempo di attraversamento del processo produttivo. La presenza di spreco, in una qualsiasi delle sue forme, porta inevitabilmente ad allungare il lead time: la sua riduzione diventa pertanto l’obiettivo strategico di primaria importanza. Ridurre il lead time consente da un lato di incrementare la flessibilità del sistema produttivo e la velocità di risposta ai clienti, e dall'altro di ridurre i costi connessi agli sprechi.
La realizzazione pratica del Just in Time richiede di introdurre tecniche specifiche di gestione della produzione, tutte rivolte a migliorare il flusso dei processi; fra queste ci sembra opportuno citare almeno le seguenti:
- Kanban
- Livellamento della produzione
- Riduzione dei tempi di Setup
- Layout delle macchine e operatori polivalenti
- Standardizzazione dei cicli di lavorazione per bilanciare le linee
- Controllo autonomo dei difetti
- Miglioramento del lavoro attraverso i suggerimenti