TPM - Total Productive Maintenance
La manutenzione è affare di tutti e si occupa di tutto.
Quanto ti costa il tuo attuale modello di manutenzione? Se includi i costi delle fermate non programmate, i guasti dell’impianto le riparazioni in urgenza e … il cliente scontento che non riceve quanto gli hai promesso in tempo, allora la risposta è: TROPPO!
Le tecnologie messe a disposizione da Industria 4.0 (IIoT sui prodotti, sensori sulle macchine, realtà aumentata, cloud e Big Data Analytics) incrementano fortemente l'efficacia delle attività di manutenzione e consentono di: rimandare investimenti in impianti e macchine, ridurre i costi di riparazione e sostituzione dei componenti, evitare interventi “di urgenza” dei tecnici e dei fornitori.
Aumento della produttività
Mantenendo lo stesso parco di impianti e macchine si liberano ore di produzione che, oggi, sono perse per interventi di riparazione. Quindi, l’efficienza della produzione si impenna
Riduzione dei costi
Diversificando le modalità di intervento di manutenzione, si riduce il costo della produzione e il costo vivo degli interventi di manutenzione. I tecnici trovano il tempo per lavorare sull’affidabilità dell’esistente
Clienti più soddisfatti
Una manutenzione più organizzata e prevedibile consente alla pianificazione della produzione di rilasciare gli ordini con maggior confidenza che vengano rispettate le date di consegna
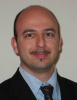
Alessandro Rolla
Sono consulente di Direzione Aziendale dal 2002
Ho aiutato più di 50 specialisti del miglioramento continuo Lean Six Sigma (Green Belt e Black Belt) ad ottenere la loro certificazione seguendoli nei loro progetti applicativi in azienda (con un saving medio a progetto superiore a 80 mila €).
Collaboro dal 2004 con il Politecnico di Milano per la Didattica Integrativa nel Dipartimento di Ingegneria Gestionale.
La mia specializzazione è sui metodi e sulle tecniche di Project Management.
Applico i modelli più attuali ed efficaci per la gestione delle commesse Engineering To Order nelle aziende manifatturiere. Ho maturato decine di esperienze nel miglioramento organizzativo ed operativo dei processi di Sviluppo Innovativo di Prodotto e di Processo in diversi settori industriali.
Puoi contattarmi e vedere i miei contributi su LinkedIn o salvare i miei contatti scansionando il QR Code a fianco
Se questo tema ti interessa e vorresti sapere come renderlo operativo in modo efficiente nella tua azienda, contattami.
Organizziamo un workshop di 4 ore sull'argomento e lo contestualizziamo sul mercato in cui operi!
E' il modo migliore per conoscerci, ci permette di ascoltare i tuoi bisogni e di capire qual è il modo migliore per raggiungere i tuoi obiettivi.
Un'iniziativa TPM (e non solo) per cogliere molte opportunità di miglioramento
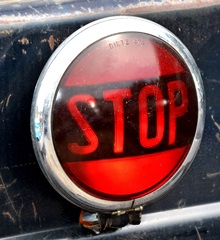
Come si applica la TPM (Total Productive Maintenance)
Esistono diversi approcci alla manutenzione:
Preventiva | l’intervento e la riparazione avviene previa stima della vita residua del componente |
---|---|
A guasto | l’intervento e la riparazione avviene solo quando si verifica il guasto |
Predittiva | l’intervento avviene su segnalazione di sensori o indicatori che precedono la rottura |
Opportunistica | i controlli e l’eventuale intervento viene svolto quando capita l’occasione di lavorare su altri componenti perché la parte dell’impianto interessata è di difficile accesso |
Con il Total Productive Maintenance si redige un piano di manutenzione per ogni macchina o impianto dell’azienda che definisca quali approcci adottare in base al reale utilizzo che viene fatto, alla storia della risorsa e alle informazioni raccolte su tutti i componenti soggetti a manutenzione.
Per attuare ciò occorre costruire una storia significativa degli impianti tale da fornire tutte le informazioni utili allo scopo:
- Anagrafica dell’impianto
- Principali eventi di manutenzione
- Comportamento dell’impianto nell'uso corrente
- Indicatori statistici (es. capability e carte di controllo) relativi alle prestazioni delle principali funzioni produttive
- Progettazione dei piani di manutenzione periodici di tutti i componenti critici per tutte le macchine
- Adeguamento del processo di pianificazione per consentire l’esecuzione dei piani
- Assegnazione delle responsabilità sulle figure organizzative interessate alla manutenzione
- Definizione del sistema di monitoraggio del piano di manutenzione definitivo
Il TPM è caratterizzato dal coinvolgimento nella manutenzione anche degli operatori: sono quelli che conoscono meglio le condizioni d’uso di un impianto e che possono intervenire più rapidamente. Non è detto che debbano eseguire in prima persona tutte le attività: sicuramente possono rilevare misure e informazioni utili per comprendere lo stato generale di usura dell’impianto affinché i tecnici manutentori possano programmare meglio i loro interventi.